Exclusive: Growing the Circular Economy with Science and Innovation
By Brett Hansard
When the world’s first fully synthetic plastic was invented a little more than a century ago, it was marketed as “the material of a thousand uses.” Designed to provide a safe, inexpensive alternative to limited natural resources, it ushered in an era of seemingly endless manufacturing possibilities.
But what was once considered a miracle of modern science is now seen in a more nuanced light. While plastics have proven indispensable in everything from medical devices and electronics to food packaging, its sheer abundance and low cost is having devastating environmental impacts.
Globally, more than 400 million metric tons of plastic are produced every year, 75 percent of which ends up in landfills, despite the recyclability of many plastic types.
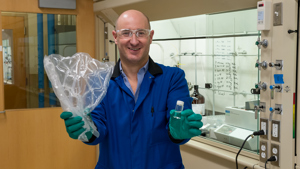
“We spent the last 100 years improving and perfecting plastic to make it the best material,” said Massimiliano “Max” Delferro, a chemist at the U.S. Department of Energy’s (DOE) Argonne National Laboratory. “Scientists are really thinking about what we are going to do with it all.”
Delferro is co-leader of the Science for a Circular Economy Initiative at Argonne that aims to spark innovations in chemical processes and materials design to facilitate the reuse of resources contained in waste.
“We are living in a linear world right now, where we use a product once and then throw it away. What we really want to do is think about how any waste can have a circularity, where it can be used and reused again, and then eventually broken down to individual pieces to decompose,” Delferro explained.
Replacing the “take, make, waste” linear economy with the more circular concept of “recovery, recycle and reuse” is not new. But the difference now is the potential for science to spur the technological innovations necessary to move in that direction.
Ultimately, the goal is for all products to be designed from the beginning to avoid waste and be less harmful, noted Cristina Negri, director of Argonne’s Environmental Science division and a part of the team behind the circular economy initiative.
“The circular economy is more than just recycling, though that’s part of it,” she said. “Fundamentally, it’s the way you approach your production processes from the outset. It means considering all end impacts in the design for the best outcome possible that respects the planet and accomplishes the intended purpose. And that’s where science is providing us with exciting new opportunities.”
Closing the Loop on Plastics
Given their ubiquity, plastics are a useful case study on how the circular economy can work in practice. According to Negri, there are two distinct cycles to circularity in plastics – one that focuses on reuse, and the other on when products enter the natural system at the end of use.
“At the outset, I want to make a molecule, break it down, reuse it and keep reusing it for as long as possible,” she said. “And then, when that piece of plastic ends up in the ocean, for example as microplastic, it has to have a way to degrade and turn into something that the environment can use and be compatible with. That can’t take hundreds of years, it has to occur in a more acceptable amount of time, because the environment is ultimately the most important circular system.”
Scientists from across Argonne, together with other research institutions, are collaborating on efforts to design new plastic materials that can be disassembled and reused.
“If you have a molecule made out of LEGOs and you cannot use it as is, you have the technology to take apart all the little LEGO bricks and recompose them into something else,” Negri explained. “In addition, the idea of ‘upcycling’ lets you use the same starting blocks to make something that has better value.”
When plastic waste gets recycled, the resulting product is generally of lower quality and value than the original plastic. A recent successful example of upcycling comes from a multi-institutional project involving Argonne along with DOE’s Ames Laboratory and researchers from leading universities. By scaling up a process used by chemical scientists to separate plastics at the molecular level, applied materials scientists are turning plastics into automotive lubricants, which have a much higher resale value.
“Our research shows that the properties of the lubricants we can make are in some cases superior to the oil that you can buy commercially,” Delferro said. “If you can recover the plastic from a landfill and make a more valuable product with better properties, then this would appeal to companies because it makes good economic sense.”
And that cost-benefit question is critical.
“That’s the key to this whole discussion,” said Negri. “It’s not just a matter of having the technology to break down these molecules into things you can reuse. It’s also, how much is this going to cost, how much energy are you going to spend doing that, and how benign to the environment is the process and its products? So that’s the system-level perspective you need for ‘circular’ to make sense.”
At the same time, Negri and her colleagues are developing an environmental framework meant to guide the creation of these new polymers and steer manufacturers away from those that pose a potential risk to the environment in terms of toxicity, persistence and mobility. While the framework will eventually embrace a number of components, the major focus right now is collecting enough data to inform a database and decision tool.
“Much in the same way we introduce engineering controls to stay safe at work, an environmentally responsible new product is one that is designed from the start to be benign in the environment,” Negri said. “We call it responsible innovation. Responsible means that when you’re making something new, you better know what its behavior is going to be across its lifecycle and understand any unintended consequences.”
Delferro is optimistic that meaningful progress on the problem of plastic accumulation can come relatively quickly. He noted that DOE and other government agencies are fully committed to the idea, while private sector companies are establishing ambitious sustainability goals.
“It won’t happen immediately, but with everyone focused on solving this problem we can do it in five to 10 years if we all work together,” he said.
Delivering Breakthrough Solutions
Plastics of course are just one part of Argonne’s investment in a circular economy. It is an interrelated series of challenges that are critical to the future of environmental preservation, national security and global industry – all at a time when the demand for raw materials and natural resources is only continuing to grow.
While still in its early stages, the initiative aims to deliver breakthrough solutions such as upcycling abundant waste materials into high-value fuels, substituting new materials that reduce the demand for precious natural resources, and reducing the impact on the environment from outdated waste disposal practices.
And according to Negri and Delferro, Argonne is uniquely qualified to take a leading role.
“We have world-class user facilities that will be critical to our success as this initiative progresses,” Negri said. She specifically pointed to the Argonne Leadership Computing Facility (ALCF), with its high-powered computers to support the use of artificial intelligence; the Advanced Photon Source (APS), to help with visualization and imaging; the Center for Nanoscale Materials (CNM), for its characterization capabilities; and the Materials Engineering Research Facility, to scale-up materials and processes.
Additionally, Delferro emphasized the range of experts residing at Argonne and their agility in working together.
“To solve these problems you need a team, and you need people with different backgrounds – from chemists, chemical engineers, environmental risk specialists, toxicologists, physicists and biologists to economists, and behavioral and political scientists,” he said. “This is exactly the kind of challenge that a national laboratory like Argonne should be trying to tackle.”
The ALCF, APS, and CNM are DOE Office of Science User Facilities.
Comments